The need to reduce wasteful spending practices is more imperative than ever before in refinery operations. Some of these revenue losses have actually been identified during unit turnarounds, where temporary generators are brought in to support maintenance tasks performed by various contractors and trades. For much of the time that the generators are on location, they are running in idle mode, wasting fuel and leading to emissions that probably would not have been of any consequence 20 years ago. However, EPA mandated Tier 4 emissions limits have changed this paradigm, which is why we are seeing more emphasis on power automation systems — even for temporary services.
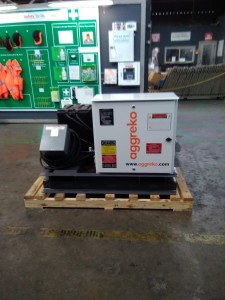
Compact hybrid battery packs integrated with a power automation system allows “big” generators to start & stop only when demand is needed.
Mobile generators brought in to support unexpected shutdowns and emergencies, such as with the recent Hurricane Harvey impacting Gulf Coast refinery operations, have benefited from power automation systems that eliminate idling and save up to 65% in fuel costs, according to estimates. The technology also reduces emissions, regardless of the fuel source. One supplier’s scalable power automation system incorporates a hybrid battery control kit that synchronizes stop and start with programmable logic controls (PLCs), tank level switches, thermostat contacts, valve actuators and other digital switches.
For one major supplier of mobile power, Aggreko PLC, their system was perfected in oil and gas operations, such as with artificial lift systems (primarily rod pumps and ESPs), midstream pumping stations and related facilities. According to one midstream operator, “we were having tons of issues with diesel engine driven generators when run at low loads, resulting in escalating reliability problems, such as when running at full loads for 30 to 90 minutes and then at idle for 30 to 90 minutes. In other instances, there were some loads where they were running 4 to 5 hours fully loaded and then 8 to 10 hours just idling. Similar start and stop operating scenarios are seen with certain refinery and petrochemical operations.
The current range of applications integrated with temporary generators, process heat exchangers, chillers, etc., increases up-time, as it reduces failures associated with overheating and excessive idle time. Citing another midstream example, one operator’s 200 hp positive displacement booster pump was moving produced oil from the field by pipeline to gathering facilities, but the pump only ran for two hours per day, so Aggreko provided a system incorporating a hybrid battery “pack” into the power automation network to provide power only when required.
In general, hybrid battery systems integrated into an overall power automation system send power to run low power consuming loads, such as communication and monitoring systems, temporary floodlighting, etc., while allowing the “industrial-sized” temporary generators to start and stop only whenever there is a a surge in demand for larger loads (e.g., circulation pumps). In addition, Aggreko’s technical experts monitor the performance of the power automation system via proprietary Aggreko Remote Monitoring (ARM) – a real-time monitoring and diagnostic service, to ensure everything runs at peak efficiency.
Leave a Reply
You must be logged in to post a comment.