A recent discussion by Grace Catalyst Technologies’ Thomas Habib on increasing propylene yields from an FCC unit processing high metals resid also made reference to the causes and consequences of high FCC regenerator temperatures, noting that high intrinsic coke selectivity (high delta coke) encountered when cracking resid raises FCC regenerator temperature, lowering cat/oil ratio and conversion.
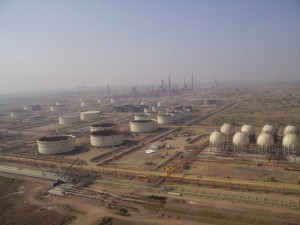
More refineries are processing resids while also targeting higher propylene yields.
Metals from resid feeds poison (deactivate) the FCC catalyst, raising regenerator temperature even higher, which further lowers cat/oil ratio and conversion. Higher catalyst addition rates are therefore required to maintain activity due to catalyst deactivation from metals, including iron (Fe) and vanadium (V), which is why IMPACT® catalyst employing a rare earth (RE) oxide-based vanadium trap is effective with resid feeds.
Fluid catalytic cracking reactions produce large amounts of gasoline range olefins. ZSM-5 selectively cracks gasoline range olefins to propylene, with some yield of butylene and other light products. ZSM-5 must be stabilized or it will quickly lose activity, but ZSM-5 stabilization requires conditions that are destructive to USY zeolite. ZSM-5 can be incorporated into a separate particle additive, but using large amounts of additive will dilute cracking catalyst, reducing activity and conversion. The entire catalyst system needs to be optimized, including the USY level, USY UCS, and the ZSM-5 content, for each individual operation.
Some resid feeds contain organic Fe, greatly reducing the bottoms cracking activity of the catalyst. For these conditions, the unit design will include catalyst coolers to lower regenerator temperature and maintain high cat/oil ratios. Regardless of desired product slate, the foundation for a superior resid cracking catalyst is metals tolerance (metal traps), coke-selectivity and bottoms cracking. There are additional issues when operating for maximum propylene with resid feeds, including:
- Conversion must remain very high, preferably beyond maximum gasoline (i.e. in overcracking) requiring high base catalyst activity
- Unit cell size (UCS) must be optimized for the specific operation
- Use of a stable, high activity ZSM-5 additive is required
- Ni present in resid feeds deposit on the catalyst exterior surface, but over time penetrates the entire catalyst particle
- Ni catalyzes coke formation and H2 production, but does not deactivate the catalyst cracking sites
- Ni can be passivated by using catalysts containing Ni traps (special aluminas) or Sb passivators.
Trapping Vanadium
Under FCC regenerator conditions, vanadium can become volatile in the form of vanadic acid (H3VO4). Many attempts have been made to trap vanadium using basic oxides, such as MgO, CaO and RE oxide. MgO- and CaO-based traps may work under laboratory deactivation conditions. However, in commercial units MgO reacts strongly with SiO2 to form Mg2SiO4 (forsterite) and CaO reacts strongly with SO3= to form CaSO4 (anhydrite).
Unlike MgO and CaO, RE oxides do not form stable silicates or sulfates under FCC regenerator conditions. They have been shown commercially to effectively trap vanadium. IMPACT® catalyst employs a RE oxide-based vanadium trap. RE oxides do not form stable compounds with silica and sulfate and thus remain available as a vanadium trap. IMPACT® catalyst is an integral catalyst, which is why it is effective even in units with low vanadium mobility.
Microprobe analysis shows vanadium to migrate to regions of high RE2O3. In comparison, MgO and MgO/CaO – based V-traps do not work, as can be demonstrated. For example, commercial Ecat was separated by density into the metals-trap fraction (“sink”) and the active catalyst fraction (“float”). The metals-trap was either MgO-based or MgO/CaO-based.
The MgO trap has very low surface area and actually contains less vanadium than the active particles. MgO readily reacts with silica, alumina or silica-alumina under hydrothermal conditions to make dense phases of forsterite (Mg2SIO4), MgAl2O4 or MgAl2Si3O10 , rendering the MgO particles ineffective as a vanadium trap. The MgO/CaO trap also has very low surface area and very high (>20%) SO4=. It picks up the same vanadium but less nickel than the base catalyst. The CaO reacts stoichiometrically with SO4= to form CaSO4 (anhydrite), rendering it inactive to trap vanadium. The MgO partially reacts with SiO2 to form forsterite. Fortunately, rare earth (La) based V-traps work. Electron microprobe analysis shows close association between La and V in Ecat.
Improving Bottoms Cracking
Fe can appear as “tramp Fe” – small particles of steel that have minimal effect, or as detrimental organic Fe. Organic Fe present in some resid feeds may lead to loss in bottoms cracking. The effect is aggravated by Ca. The problem is characterized by formation of nodules and a glassy skin on the surface of the Ecat, which lowers diffusivity. High porosity, high MSA catalysts such as the Grace Midas® catalyst can minimize the effect of Fe catalyst poisoning in FCC reactor conditions targeting propylene maximization.
Organic Fe is present in some resid feedstocks. Fe from feed can deposit on the catalyst exterior surface, causing glassy nodules that restrict diffusion into the particle. As previously emphasized, high porosity, high MSA catalysts such as Midas® can minimize these detrimental effects. Within the context of potential metals contamination problems that may be encountered when maximizing propylene production with resid feeds, operating conditions favoring propylene include low hydrocarbon partial pressure and high conversion (high cat/oil, high reactor temperature). Catalyst properties favoring propylene production include:
- High activity
- UCS effect is mixed: lower UCS favors olefins but higher UCS gives higher activity and conversion
- UCS should be optimized considering the entire catalyst system, feed and operation
- High concentration of stabilized ZSM-5 (OlefinsUltra-HZ® additive is the highest ZSM-5 content, fully stabilized olefins additive available).
Editor’s note: This article is based on a presentation from the Hydrocarbon Publishing Third Opportunity Crudes Conference held in Houston and preceded by another article focusing on propylene production published in Vol. III, No. 10 of Refinery Operations, “Increasing Resid to Propylene Yields,” by E. Thomas Habib, Jr (tom.habib@grace.com).
Leave a Reply
You must be logged in to post a comment.